Vision 2030 for Vietnam GMT Sector $100 billion
Vietnam’s $100 billion garment sector is on a promising trajectory, set to reach this ambitious milestone by 2030 according to VietnamCredit. McKinsey emphasizes the sector’s potential for sustainable growth, aligning with Vietnam’s net-zero goals. The digitalization drive, as outlined in VietnamNet, will further enhance efficiency and competitiveness. Vietnam’s robust export-import industries, as noted in Vietnam Briefing, provide a solid foundation for the sector’s expansion. With strategic investments in sustainability, technology, and digitalization, Vietnam’s garment industry is poised for continued success and significant contributions to the economy.
Vietnam’s garment industry has emerged as a global powerhouse, with ambitious targets set for the future. According to Prime Minister Pham Minh Chinh, Vietnam aims to achieve $100 billion in textile exports by 2030, showcasing the sector’s significant growth and potential. This growth trajectory is supported by various factors, including a skilled workforce, competitive production costs, favorable trade agreements, and a strategic geographical location that facilitates efficient supply chains and access to key markets.
Statista’s outlook on Vietnam’s textile industry underscores this growth trend, with the value added in the sector projected to reach US$21.12 billion by 2024. The apparel market in Vietnam is also experiencing substantial revenue growth, with segments such as men’s and women’s wear, children’s wear, and sportswear driving the industry forward.
A detailed report by the World Fashion Exchange highlights Vietnam’s evolving textile and garment industry, emphasizing its increasing attractiveness for global brands and investors. The report delves into various aspects such as manufacturing capabilities, export trends, sustainability initiatives, and the integration of technology to enhance productivity and quality.
Challenges faced by Vietnam in Capacity building of human resource
- Focus on Basic Skills: One of the foremost challenges faced by Vietnam’s textile and garment industry is the scarcity of skilled labor. A study from Suntech Textile Machinery identifies a shortage of workers with essential skills, necessitating focused efforts on basic skill enhancement. To address this challenge, the industry must prioritize foundational training programs covering core competencies like machine operation, quality control, and production processes. Collaborations with vocational institutions and on-the-job training initiatives can bridge the skills gap and ensure a proficient workforce.
- Limited Training Infrastructure: Vietnam’s textile and garment sector encounters limitations in training infrastructure, hindering effective capacity building endeavors. Insights from IntechOpen emphasize the need for modernized training facilities to facilitate skill development and retention. Overcoming this challenge requires investments in state-of-the-art training centers equipped with technology-enabled learning environments. Public-private partnerships can play a pivotal role in expanding training infrastructure and ensuring access to cutting-edge resources for effective skill acquisition.
- Short-Term vs. Long-Term Focus: Balancing short-term operational goals with long-term talent development is a persistent challenge in Vietnam’s textile and garment industry. A report from Vietnam Briefing underscores the importance of aligning strategic objectives with sustainable human resource development. To surmount this challenge, industry stakeholders must prioritize long-term talent development strategies, including career progression pathways, continuous learning initiatives, and leadership development programs. This strategic shift can foster a culture of innovation, resilience, and competitiveness.
- High Turnover and Limited Investment in Upskilling: Vietnam’s textile and garment sector grapples with high turnover rates and inadequate investments in upskilling initiatives. Findings from ResearchGate highlight the urgent need for comprehensive talent retention and upskilling strategies. To mitigate turnover and promote skill enhancement, industry players should invest in competitive compensation packages, performance-based incentives, and ongoing training programs. Emphasizing employee engagement, career growth opportunities, and digital skills development can foster a loyal and skilled workforce.
- Digital Literacy Gap and Limited Resources for Digital Training: The digital literacy gap and constraints in digital training resources pose significant challenges in Vietnam’s textile and garment industry. Studies from Abacademies underscore the imperative of addressing digital skills shortages and fostering a tech-savvy workforce. To bridge the digital divide, the industry should implement targeted digital skills training programs, leverage digital learning platforms, and collaborate with tech providers for customized solutions. Government support and industry partnerships can alleviate resource constraints and facilitate effective digital training initiatives.
Suggestions to overcome those challenges/How other competitors are handling the same issue
- Continuous Performance Evaluation and Feedback: Conduct regular performance evaluations and provide constructive feedback to employees for continuous improvement. Implement performance-based incentives and recognition programs to motivate and retain high-performing talent.
- Sustainable Talent Management Practices: Implement sustainable talent management practices focused on diversity, inclusion, and employee well-being. Incorporate sustainable development goals (SDGs) into talent management strategies for a more resilient and responsible workforce.
- Public-Private Partnerships for Capacity Building: Foster collaborations between government agencies, industry associations, and private enterprises to drive capacity building initiatives. Establish industry-academic partnerships for knowledge sharing, research collaborations, and talent development programs.
- Strategic Talent Acquisition and Retention: Implement targeted recruitment strategies to attract skilled professionals for middle management, floor management, and industrial engineering roles. Offer competitive compensation packages, career advancement opportunities, and employee retention programs to reduce turnover rates.
- Investment in Comprehensive Training: Allocate resources for specialized training programs covering basic skills and advanced competencies. Learn from competitors like China and India, who prioritize continuous skill development and talent retention.
- Long-Term Talent Development: Foster a culture of continuous learning, career progression, and leadership development to retain skilled employees and drive innovation.
- Digital Transformation: Embrace digital technologies for efficient training delivery, digital literacy enhancement, and upskilling initiatives. Learn from advanced manufacturing hubs like South Korea and Germany to integrate digital tools seamlessly into operations.
By implementing these strategies and leveraging competitor insights, Vietnam’s textile and garment industry can overcome capacity building challenges effectively, empower its workforce, and strengthen its position in the global market.
How Groyyo can be the key contributor to overcome these challenges
Vietnam’s garment industry is at a crossroads, facing challenges in human resource development that are crucial for its sustainable growth. Amidst these challenges, consulting companies like Groyyo emerge as key contributors in overcoming obstacles and empowering the industry’s workforce. Here’s how Groyyo can play a pivotal role:
- Comprehensive Training Solutions: Groyyo specializes in designing and implementing comprehensive training solutions tailored to the specific needs of the garment industry. By focusing on basic skills enhancement, advanced technical training, and digital literacy programs, Groyyo equips workers with the capabilities necessary for modern manufacturing practices.
- Strategic Planning for Long-Term Success: Groyyo’s expertise lies in strategic planning, helping companies in the garment sector balance short-term production demands with long-term skill development goals. Through strategic workforce planning, Groyyo assists in identifying talent gaps, implementing retention strategies, and fostering a culture of continuous learning.
- Digital Transformation Support: As digitalization reshapes the garment industry, Groyyo offers invaluable support in navigating this transformation. From digital skills training to integrating innovative technologies like IoT and automation, Groyyo empowers companies to stay ahead in the digital age and remain competitive on a global scale.
- Collaborative Partnerships: Groyyo believes in the power of collaboration. By fostering partnerships between industry stakeholders, educational institutions, and government bodies, Groyyo creates ecosystems that facilitate knowledge exchange, skills development, and resource sharing for the benefit of the entire industry.
- Data-Driven Insights: Leveraging data analytics and industry insights, Groyyo provides data-driven recommendations and strategies for optimizing human resource management practices. From talent acquisition to performance management, Groyyo’s analytical approach enhances decision-making and drives continuous improvement.
- Sustainability and Ethical Practices: Groyyo recognizes the importance of sustainability and ethical practices in today’s garment industry. Through training programs focused on sustainable manufacturing practices, ethical sourcing, and compliance with international standards, Groyyo helps companies build responsible and resilient supply chains.
Benefits of Capacity building to the Garment Manufacturing sector in Vietnam
Capacity building plays a crucial role in enhancing the competitiveness, sustainability, and resilience of Vietnam’s garment manufacturing sector. Through strategic investments in skills development, technology adoption, and sustainable practices, capacity building initiatives yield a range of benefits that contribute to the sector’s long-term success and positive impact on the economy. Key benefits of capacity building in Vietnam’s garment industry:
- Enhanced Productivity and Efficiency: Capacity building programs focusing on skill development and training lead to a more skilled and knowledgeable workforce. According to the United Nations ESCAP’s report on capacity building for sustainable development, investing in human capital results in increased productivity and efficiency within the garment manufacturing sector. Workers equipped with advanced technical skills, digital literacy, and knowledge of modern production techniques can perform tasks more effectively, reducing production costs and improving overall output quality.
- Adaptation to Technological Advancements: The garment industry is evolving rapidly, driven by technological advancements such as automation, IoT, and data analytics. A capacity building plan for Vietnam, as outlined in Carbon Limits’ project, includes initiatives to build technical expertise and foster innovation within the sector. By embracing new technologies and equipping workers with the necessary skills, garment manufacturers can stay ahead of market trends, streamline operations, and meet the demands of increasingly digitalized supply chains.
- Compliance with Environmental Standards: Greening Vietnam’s textile and garment sector, as discussed in Better Work’s article, is a critical aspect of capacity building. Training programs focused on sustainability practices, resource efficiency, and eco-friendly production methods help companies reduce their environmental footprint. By adopting greener processes and adhering to international environmental standards, garment manufacturers not only contribute to environmental conservation but also enhance their reputation as responsible and ethical businesses, attracting environmentally conscious consumers and investors.
- Access to International Markets: Capacity building initiatives also facilitate market access and competitiveness on a global scale. The United Nations ESCAP report emphasizes that a skilled workforce and adherence to quality standards are essential for exporting to international markets. Through capacity building, Vietnam’s garment manufacturers can meet the stringent requirements of global buyers, penetrate new markets, and diversify their customer base, thus boosting exports and economic growth.
- Resilience to Challenges: Building resilience is another key benefit of capacity building. In a rapidly changing business environment, equipped with knowledge, skills, and adaptable practices, garment manufacturers can better navigate challenges such as market fluctuations, supply chain disruptions, and regulatory changes. Capacity building fosters a culture of continuous learning and improvement, empowering companies to innovate, problem-solve, and sustain long-term success.
In conclusion, capacity building initiatives are instrumental in unlocking the full potential of Vietnam’s garment manufacturing sector. From increased productivity and technological adaptation to environmental sustainability, market access, and resilience, the benefits of capacity building extend across various aspects of the industry, contributing to its growth, competitiveness, and positive impact on the economy.
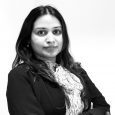
Leave a Comment