Vietnam’s apparel industry is at a pivotal stage of growth, with increasing global demand driving the need for high-quality, efficient production. While the country is one of the world’s leading exporters of garments, challenges like skill shortages and productivity gaps are becoming increasingly apparent, particularly in the higher-value segments of the supply chain.
Vietnam Industry Report 2023 highlighted that productivity in Vietnam’s apparel sector lags behind competitors such as China and Bangladesh, despite the country’s large workforce. This disparity is not due to a lack of resources but to a shortage of training programs focused on workforce development, operational excellence, and continuous improvement.
To sustain this growth and meet the evolving demands of international buyers, Vietnam’s apparel manufacturers must address these key challenges head-on. At Groyyo Consulting, we recognize that productivity and skill development are the cornerstones for Vietnam’s continued success in the global apparel market.
The Challenge: Productivity Gaps and Skill Shortages
Vietnam’s apparel sector has seen impressive growth, with exports surpassing $40 billion in recent years. However, this success has highlighted certain weaknesses. The industry is facing critical gaps in worker productivity, particularly when compared to competitors like China and Bangladesh, who have been adopting more advanced techniques and innovations.
According to the Vietnam Textile and Apparel Association (VITAS), while the Vietnamese workforce is vast, its overall productivity per worker remains lower than regional peers. This challenge is compounded by the increasing complexity of apparel production, especially in the higher-value segments such as fashion-forward apparel and technical textiles.
Skill shortages represent another significant hurdle. Many Vietnamese factories lack adequately trained workers to handle complex garment designs or adopt modern production techniques. This issue is most pronounced in the middle management layer, where the skill gap is slowing down efforts to optimize production lines and implement international quality standards.
Groyyo Consulting: A Strategic Partner for Workforce Enhancement
Though relatively young, Groyyo Consulting has made significant strides in supporting apparel manufacturers in India and Bangladesh over the last three years. With a sharp focus on elevating productivity and empowering workforces, our approach is designed to create scalable and long-lasting improvements for factories that aim to compete at the highest level.
While Groyyo Consulting doesn’t currently have formal partnerships with VITAS or development agencies in Vietnam, we’ve worked with various stakeholders across the region to understand the unique needs of manufacturers. We bring a wealth of practical, hands-on experience to the table, derived from our engagements with clients across the textile and apparel sectors in the broader Southeast Asian region.
Here’s how Groyyo Consulting can assist Vietnamese manufacturers:
- Comprehensive Skill Development Programs
At the heart of any productivity improvement initiative is workforce development. Groyyo Consulting offers tailored training programs that equip factory workers, supervisors, and managers with the skills they need to excel in modern apparel manufacturing. Our training programs are not one-size-fits-all; instead, they are customized to meet the specific challenges that each factory faces, whether it’s a shortage of skilled operators or the need for enhanced middle management capabilities.
We focus on:
- 1. On-the-floor operator training to ensure seamless integration of high-value apparel production processes.
- 2. Supervisor and management development programs that equip middle management with tools to streamline operations, enhance communication, and adopt global best practices.
- 3. Training modules on international quality standards and compliance, ensuring Vietnamese manufacturers can meet the expectations of global buyers.
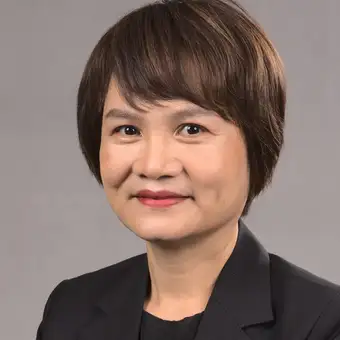
Factory Productivity Improvements
Improving productivity requires a holistic approach that looks beyond mere labor output. Groyyo Consulting specializes in helping manufacturers optimize factory layouts, production processes, and workflows to reduce inefficiencies and increase output without compromising quality.
Some of the core productivity improvement strategies we offer include:
- Lean manufacturing implementation: By eliminating waste, streamlining operations, and optimizing material flow, we help factories significantly increase their production capacity.
- Time and motion studies: Groyyo Consulting’s experts conduct thorough assessments of production lines, identifying bottlenecks and recommending ways to minimize downtime and boost overall efficiency.
- Workplace organization: Proper organization of tools, equipment, and materials is vital to maintaining a smooth production flow. We assist in organizing production floors to enhance productivity and safety.
“By focusing on lean practices and continuous improvement, we’ve seen remarkable results across factories in Southeast Asia,” says Abhishek Yugal, Managing Partner of Groyyo Consulting. “Vietnamese manufacturers are no different, and with the right interventions, they can significantly improve their operational efficiency.”
- Leadership and Middle-Management Empowerment
One of the most overlooked aspects of factory improvement is the role of middle management. In many Vietnamese factories, supervisors and middle managers lack the necessary skills to handle increasingly complex production processes or lead large teams effectively. This bottleneck limits the factory’s ability to scale productivity and improve quality.
Groyyo Consulting emphasizes leadership training for middle management, equipping them with decision-making frameworks, conflict resolution techniques, and process improvement strategies that help unlock higher levels of productivity across the workforce.
We also engage with senior leadership teams to ensure that factory-wide initiatives for productivity enhancement and skill development are implemented cohesively and with long-term sustainability in mind.
- Long-Term Strategy for Growth
While addressing immediate productivity gaps is crucial, we at Groyyo Consulting believe in implementing solutions that have a lasting impact. Our goal is to ensure that the improvements we bring to factories are scalable and sustainable. Whether it’s through continuous workforce development, implementing lean processes, or engaging with leadership teams, we help apparel manufacturers in Vietnam establish a solid foundation for future growth.
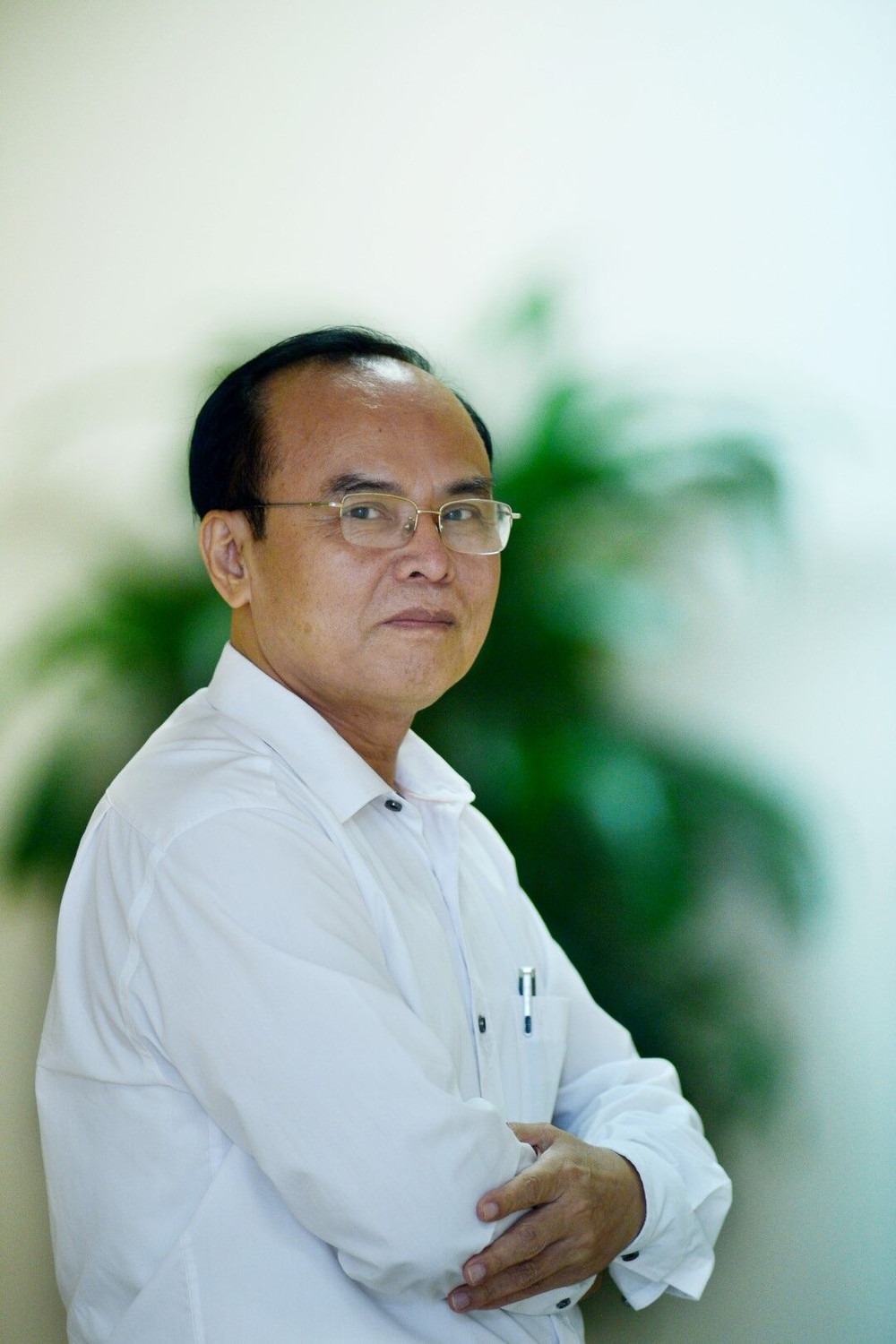
The Path Forward for Vietnam’s Apparel Industry
As Vietnam continues to solidify its position as a key player in the global apparel industry, overcoming the challenges of workforce skill shortages and productivity gaps will be essential. Groyyo Consulting is committed to being a part of this journey, offering customized, actionable solutions that enhance the productivity of factories while empowering the workforce with the skills needed for long-term success.
Our tailored approach, grounded in experience and driven by a deep understanding of the apparel sector, ensures that we can meet the unique needs of Vietnamese manufacturers. Whether it’s optimizing factory layouts, conducting productivity assessments, or providing in-depth workforce training, Groyyo Consulting is dedicated to assisting Vietnam’s apparel industry unlock its full potential.
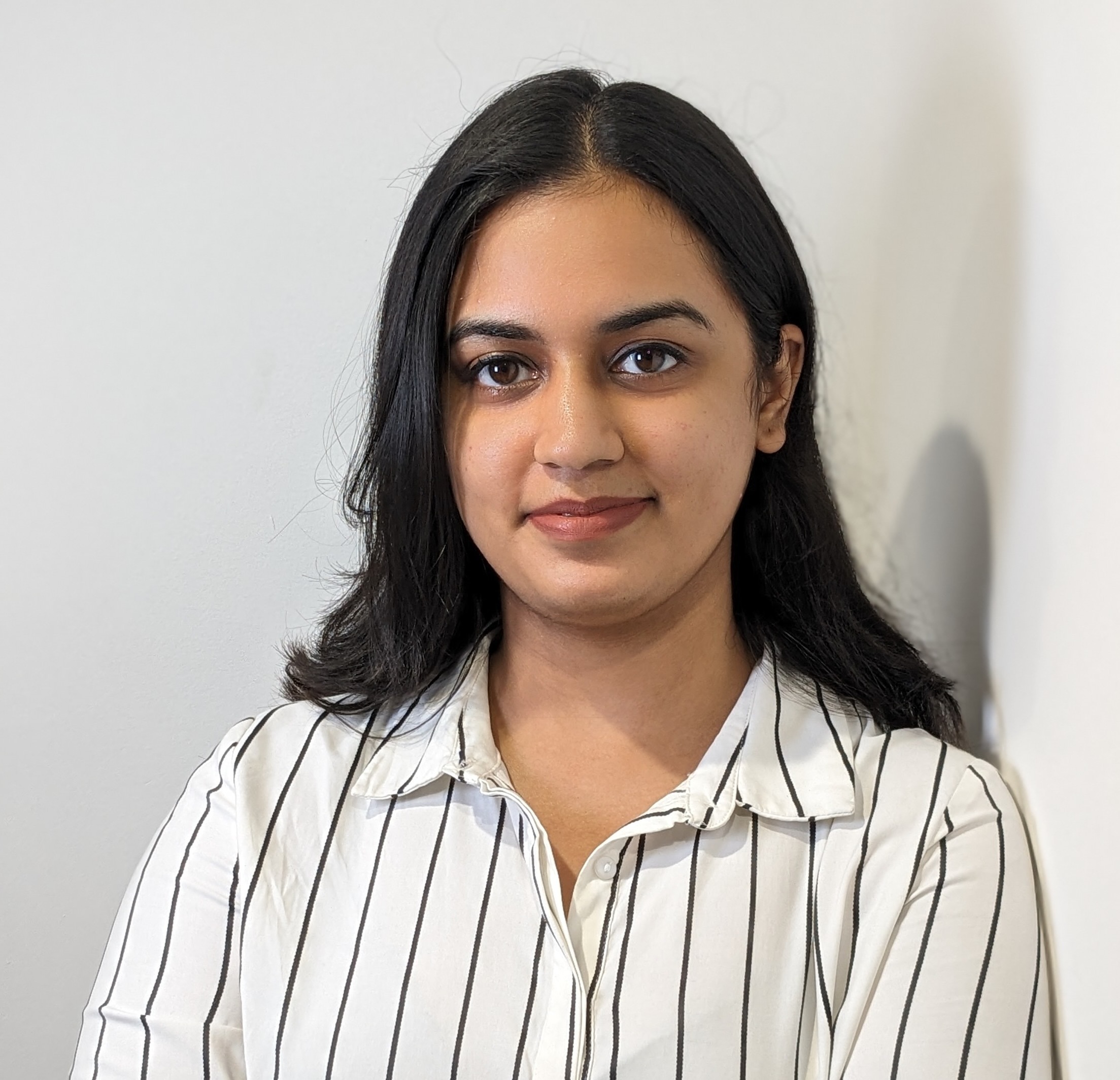
Leave a Comment