Vision 2030 for Bangladesh Gmt Sector $100 billion
Considering our world’s reliance on fashion and sartorial expressions, have we ever reflected on the industry that propels it forward? Third-world countries like Bangladesh, known for their inexpensive labor, play a significant role in manufacturing these garments. Let’s dive deep into the intricacies of this industry in greater detail. Bangladesh’s garment sector has set an ambitious goal of achieving $100 billion in apparel exports by 2030, building on its recent robust performance. The industry’s future growth prospects are promising, driven by a combination of factors such as cost-effectiveness, skilled labor force, and a conducive business environment. Bangladesh has prioritized the development of its workforce, investing in training programs and skill enhancement initiatives. This focus on human capital has not only improved productivity and efficiency but has also contributed to creating sustainable employment opportunities and uplifting livelihoods across the country.
As Bangladesh looks towards the future, sustainability and ethical practices are gaining prominence within the garment industry, initiatives aimed at reducing environmental impact, promoting fair labor practices, and ensuring worker safety are being increasingly integrated into the industry’s operations.
In essence, Bangladesh’s garment industry’s journey reflects a compelling narrative of growth, innovation, and resilience. By leveraging its strengths, addressing challenges, and embracing global trends, Bangladesh continues to carve a distinctive identity as a powerhouse in the global apparel market, poised for continued success and sustainable growth.
Capacity building in Bangladesh’s garment industry has been a transformative force, evidenced by its staggering economic contributions and global prominence. Last year, Bangladesh’s apparel exports achieved a significant milestone, reaching an unprecedented high of nearly $47 billion. This amount surpassed the previous record set in 2022 by approximately 10.27%, as reported by the Export Promotion Bureau (EPB). Employing more than 4 million people directly, as reported by Mordor Intelligence, the industry stands as the largest employment provider in the country.
Moreover, Bangladesh has solidified its position as the second-largest apparel exporter globally, capturing around 6.4% of the market share, according to Gitnux’s industry statistics. This substantial market presence highlights Bangladesh’s capacity for cost-effective production, efficient supply chain management, and market competitiveness.
However, the industry’s growth has not been without challenges. Issues such as factory safety standards and worker rights have garnered international attention, leading to initiatives like the Bangladesh Accord on Fire and Building Safety. These efforts have resulted in significant improvements in workplace safety and sustainability practices, showcasing the industry’s commitment to capacity building beyond mere economic metrics.
Challenges faced by Bangladesh in Capacity building of human resource
Bangladesh’s garment industry, a vital contributor to the economy, faces a spectrum of challenges in building the capacity of its human resources, especially in middle management, floor management, and industrial engineering management. This article explores these challenges and proposes strategies based on insights from industry experts and competitor approaches.
1. Focus on Basic Skills: The industry confronts a pressing need to address basic skills among its workforce. Studies from Textile Today reveal that a significant portion of garment workers lack proficiency in fundamental operations, highlighting the urgency for targeted skill enhancement programs. To tackle this challenge, the industry can implement specialized training modules focusing on basic skills such as machine operation, quality control, and production processes. Collaborations with vocational training institutes and on-the-job training initiatives can facilitate skill development and ensure a competent workforce.
2. Limited Training Infrastructure: Limited training infrastructure poses a considerable obstacle to effective capacity building efforts. Reports from Fibre2Fashion emphasize the need for modern training facilities equipped with technology-enabled learning environments to enhance skill acquisition and retention. To overcome this challenge, investments in state-of-the-art training centers and virtual learning platforms are imperative. Public-private partnerships can play a crucial role in expanding training infrastructure and providing access to cutting-edge resources for skill development.
3. Short-Term vs. Long-Term Focus: The industry’s short-term focus on meeting immediate production targets often hampers long-term capacity building initiatives. Insights from Asia Business Outlook underscore the importance of balancing operational goals with strategic investments in training and talent development. To address this challenge, industry stakeholders must prioritize long-term talent development strategies, including career progression pathways, continuous learning opportunities, and leadership development programs. Aligning organizational objectives with employee growth and development can foster a culture of innovation and sustainability.
4. High Turnover and Limited Investment in Upskilling: High turnover rates and limited investment in upskilling pose significant challenges to capacity building. Studies from The Hindu highlight the impact of low wages and insufficient career advancement opportunities on employee retention and skill development. To mitigate turnover and promote upskilling, industry players can adopt competitive compensation packages, performance-based incentives, and ongoing training programs. Investing in employee engagement initiatives and talent retention strategies can enhance workforce stability and expertise.
5. Digital Literacy Gap and Limited Resources for Digital Training: The digital literacy gap and limited resources for digital training present critical challenges in an era of rapid digitalization. Insights from Emerald Insight emphasize the importance of addressing digital skills shortages and leveraging technology for efficient training delivery.
Suggestions to overcome those challenges:
1. Investment in Comprehensive Training: Allocate resources for specialized training programs targeting basic skills and advanced competencies. Learn from competitors like Vietnam and India, who prioritize skill development across all levels of the workforce.
2. Public-Private Partnerships: Collaborate with government agencies, educational institutions, and industry associations to expand training infrastructure and access to learning resources.
3. Long-Term Talent Development: Foster a culture of continuous learning, career progression, and leadership development to retain skilled employees and drive innovation.
4. Digital Transformation: Embrace digital technologies for efficient training delivery, digital literacy enhancement, and upskilling initiatives. Learn from advanced manufacturing hubs like South Korea and Germany to integrate digital tools seamlessly into operations.
How Groyyo can be the key contributor to overcome these challenges
Comprehensive Training Solutions:
Groyyo Consulting can design and implement comprehensive training programs tailored to the specific needs of Bangladesh’s garment industry. By focusing on advanced skills development, these programs can bridge the gap between basic skills and industry requirements, addressing the challenge of overreliance on rudimentary skills.
Investment in Training Infrastructure:
Groyyo Consulting can advise and assist garment factories in investing in dedicated training infrastructure. This includes setting up modern training facilities equipped with state-of-the-art technology and resources to deliver high-quality training programs, overcoming the scarcity highlighted in McKinsey’s report.
Long-Term Skill Development:
By emphasizing long-term skill development over short-term gains, Groyyo Consulting can help the industry shift its focus towards nurturing a highly skilled workforce. Through strategic planning and initiatives, the consultancy can guide companies in prioritizing investments in advanced training programs aimed at continuous innovation and growth.
Reducing Turnover Rates:
Groyyo Consulting’s expertise in human resource management can assist garment factories in implementing strategies to reduce turnover rates. This includes developing retention programs, providing career development opportunities, and fostering a positive work environment to retain experienced talent and minimize disruptions in skill development initiatives.
Upskilling Initiatives:
Groyyo Consulting can work with industry stakeholders to advocate for increased investment in upskilling initiatives. By showcasing the benefits of formal training programs, the consultancy can encourage more garment factories to provide opportunities for workers to acquire new skills and advance in their careers.
Digital Literacy and Training:
Groyyo Consulting can collaborate with industry leaders to address the digital literacy gap among garment workers. This includes designing digital training modules, promoting digital literacy awareness campaigns, and facilitating access to digital training resources to enhance workers’ proficiency in digital tools and technologies.
Strategic Partnerships and Collaborations:
Leveraging its network and expertise, Groyyo Consulting can facilitate strategic partnerships and collaborations between garment factories, educational institutions, and international organizations. These partnerships can unlock funding opportunities, access to best practices, and knowledge sharing platforms to accelerate capacity building initiatives effectively.
Benefits of Capacity building to the Garment Manufacturing sector in Bangladesh
1. Enhanced Skill Levels: Capacity building initiatives lead to an enhancement in the skill levels of workers within the garment manufacturing sector. By focusing on advanced training programs, workers can acquire specialized skills that are aligned with industry requirements, thus improving their productivity and efficiency in various manufacturing processes.
2. Improved Workplace Safety: Capacity building efforts often include training on safety protocols and practices. This results in a safer working environment for garment workers, reducing the risk of accidents and injuries. Initiatives like the Bangladesh Accord on Fire and Building Safety have been instrumental in improving workplace safety standards in the industry.
3. Increased Innovation and Adaptability: Investing in long-term skill development fosters a culture of innovation within the sector. Workers with advanced skills are better equipped to handle complex tasks, embrace technological advancements, and contribute ideas for process optimization and product innovation, driving overall industry growth and competitiveness.
4. Digital Transformation: Capacity building extends to digital literacy and training, enabling workers to adapt to digital workflows and technologies effectively. Enhanced digital literacy opens up avenues for process automation, data-driven decision-making, and implementation of Industry 4.0 practices, enhancing overall efficiency and competitiveness in the digital era.
5. Industry Reputation and Compliance: Capacity building initiatives focused on sustainability, ethical practices, and compliance with international standards contribute to enhancing the industry’s reputation globally. Improved workplace conditions, adherence to labor rights, and environmental sustainability practices positively impact the perception of Bangladesh’s garment sector among international stakeholders and consumers.
6. Strategic Partnerships and Collaborations: Capacity building fosters strategic partnerships and collaborations between industry players, educational institutions, and development agencies. These partnerships facilitate knowledge sharing, access to best practices, and collaborative efforts towards addressing common challenges, driving collective growth and development within the sector.
In conclusion, capacity building initiatives bring a multitude of benefits to Bangladesh’s garment manufacturing sector, ranging from enhanced skill levels and workplace safety to increased innovation, digital transformation, and industry reputation. Embracing these initiatives is essential for sustaining growth, fostering a skilled workforce, and maintaining competitiveness in the global garment market.
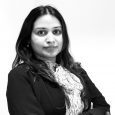
Leave a Comment