Introduction
Vietnam’s garment industry has undergone a remarkable transformation in recent decades, emerging as a global powerhouse. Driven by factors like low labor costs and strategic free trade agreements (FTAs) (Vietnam Briefing, 2023), Vietnam has become a garment export leader. The sector boasts a workforce exceeding 3 million and contributes significantly to the national economy. In 2022 alone, garment exports reached a staggering US$36.9 billion (Vietnam Briefing, 2023). This impressive trajectory is projected to continue, with Statista forecasting steady market growth in the coming years (Statista Apparel – Vietnam, 2024).
The Importance of Backward Linkage
Vietnam’s garment industry hums with the whir of sewing machines and the promise of a thriving economy. Yet, beneath the surface lies a hidden vulnerability – a dependence on imported raw materials. A significant portion of raw materials are currently imported, raising concerns about long-term sustainability and vulnerability to external factors (Smith, E., 2023). This highlights the importance of “backward linkage,” that emphasizes domestic sourcing of raw materials.
By fostering a thriving domestic textile sector, Vietnam can relieve itself from import dependence, fortifying its supply chain. This transformation unlocks not only long-term stability but also the potential for a jobs boom, further enriching the nation’s economic tapestry (Vietnam Briefing, 2023). Recognizing this transformative potential, Vietnam’s government has charted a course – a strategic plan outlined in the aptly named “Vietnam textile and garment industry development strategy to 2030, vision to 2035.” This roadmap paves the way for a more self-reliant future, where Vietnam’s garment industry can truly blossom, not just as a global exporter, but as a self-sustaining powerhouse.
Current Landscape of Raw Material Procurement
Vietnam’s current raw material procurement landscape reflects a mix of domestic production and imports. Though local production provides a foundation of cotton and other materials (Textile Today, 2023), a significant portion arrives from foreign shores. This dependence casts a long shadow, especially as the world’s insatiable appetite for apparel promises a surge in demand for raw materials (Statista 2024).
Vietnam’s garment industry has achieved remarkable success, but for long-term viability, a focus on backward linkage is crucial, which isn’t just about plugging a leak; it’s about establishing a robust domestic textile sector that forms the cornerstone of a sustainable garment industry.
Challenges Faced by Vietnam in Backward Linkage
Vietnam’s garment industry shines brightly on the global stage, its export figures a testament to its impressive production capabilities. However, a closer look reveals a hidden thread – a dependence on imported raw materials that threatens to unravel the industry’s long-term sustainability. Vietnam must embark on a path of “backward linkage,” a strategic shift towards domestic sourcing of raw materials. But this journey is not without its challenges. Let’s explore the obstacles Vietnam must overcome to solidify its position as a self-sufficient garment powerhouse.
1. Dependence on Imports: A Multifaceted Threat
- Price Fluctuations and Supply Chain Disruptions: Vietnam’s dependence on imported fabric exposes it to the whims of global markets. Price hikes in key producing countries like China can significantly impact Vietnamese garment manufacturers’ profitability, hindering production and potentially leading to missed deadlines.
- Limited Product Range: A heavy reliance on imports restricts the variety of fabrics and materials available to Vietnamese manufacturers. This limits their ability to cater to the diverse needs of global brands and adapt to evolving fashion trends (Textile Focus, 2023).
2. Quality and Standardization: A Missed Mark
- Inconsistency and Reputational Risk: Inconsistent quality within Vietnam’s domestic textile sector is a major concern (Pertiwi et al., 2017). Fluctuations in fabric quality can lead to production delays, product defects, and ultimately, reputational damage for Vietnamese garment manufacturers. This inconsistency hinders their ability to compete with established players known for high-quality products.
- Meeting International Standards: Many global brands have strict quality and sustainability standards for their garments. The lack of standardized production processes and certifications within Vietnam’s domestic textile sector makes it difficult for Vietnamese manufacturers to consistently meet these requirements, potentially limiting their access to lucrative markets (RCAPS, 2007).
3. Technological Gap: A Hurdle to Innovation
- Outdated Machinery and Inefficient Processes: Vietnam’s domestic textile industry is often characterized by outdated machinery and a lack of automation (Nghiem et al., 2014). This not only reduces production efficiency but also limits the ability to produce high-quality, intricate fabrics increasingly demanded by global brands.
- R&D Investment Deficit: Limited investment in research and development (R&D) within the domestic textile sector hinders innovation and the development of new, advanced fabrics. This puts Vietnamese manufacturers at a disadvantage compared to competitors (Investment Monitor, 2023).
4. Infrastructure Bottlenecks: A Logistical Nightmare
- Transportation Network Woes: Inadequate transportation infrastructure, including limited highways and underdeveloped rural roads, creates logistical challenges for sourcing and transporting domestically produced textiles (IDS, 2018).
- Logistics System Inefficiency: Streamlining customs procedures and improving warehousing facilities can significantly improve the efficiency of sourcing domestically produced materials (Trade Economics, 2016).
Suggestions to Overcome the Challenges Faced by Vietnam in Backward Linkage
Potential solutions to address the challenges Vietnam faces in achieving backward linkage, or domestic sourcing of raw materials for its garment industry.
1. Fostering a Thriving Domestic Production Sector
- Targeted Government Incentives: The government can play a crucial role by offering targeted financial aid, tax breaks, and subsidies specifically for modernizing machinery and infrastructure within the domestic textile sector (Nghiem et al., 2014). Prioritizing investments in areas like spinning, weaving, and dyeing can create a balanced domestic supply chain.
- Focus on Industry-Specific Research and Development: Increased investment in R&D should be directed towards developing new, high-value fabrics and production processes tailored to the specific needs of the garment industry. This could involve fostering collaboration between universities, research institutions, and textile companies (Investment Monitor, 2023).
2. Enhancing Quality and Standards for Global Competitiveness
- Standardization with International Benchmarking: Implementing quality standards that align with internationally recognized benchmarks like OEKO-TEX or Global Organic Textile Standard (GOTS) can establish trust with international brands (Pertiwi et al., 2017).
- Multi-Tiered Skill Development Programs: Skill development programs should cater to different levels within the workforce. Upskilling existing workers in quality control techniques can minimize production rejects. Additionally, introducing vocational training programs for a new generation of textile professionals can ensure a skilled talent pool for the future (ResearchGate, 2021).
3. Upgrading Infrastructure to Bridge the Logistical Gap
- Strategic Infrastructure Investment: Investments should prioritize developing logistics hubs and modernizing transportation networks, particularly in areas with high concentrations of textile production.
- Streamlining Logistics Processes: Reducing bureaucratic hurdles at customs, along with digitalization of trade documentation, can expedite the movement of domestically sourced materials. Additionally, promoting private sector participation in developing and managing modern warehousing facilities can enhance efficiency (Trade Economics, 2016).
4. Building Strong and Collaborative Supplier Networks
- Digital Collaboration Platforms: Establishing online platforms that connect garment manufacturers with domestic textile producers can foster transparency and efficient communication (Textile Focus, 2023). This allows for real-time order tracking, inventory management, and better forecasting of demand.
- Contract Farming with Risk-Sharing Models: Implementing contract farming models with clearly defined pricing and quality standards can benefit both parties. These models can provide a guaranteed market for cotton or other fiber producers while offering garment manufacturers a reliable source of raw materials (World Bank, 2015). Risk-sharing mechanisms can be incorporated to mitigate potential fluctuations in cotton prices.
5. Promoting Sustainability for Long-Term Growth
- Investment in Eco-Friendly Practices: The government and industry leaders, in order to enhance Vietnam’s global image as an environmentally conscious producer, can encourage the adoption of sustainable practices, such as organic cotton production and water-efficient dyeing techniques (Textile Today, 2023).
- Capacity Building for Sustainable Certification: Supporting domestic textile producers in achieving international sustainability certifications like Fairtrade or Better Cotton Initiative (BCI) can unlock access to premium markets with strict ethical and environmental sourcing requirements. This can involve providing financial and technical assistance to producers (Textile Today, 2023).
How Groyyo can be the key contributor to overcome these challenges
Vietnam’s garment industry, a powerhouse in exports, faces a critical crossroads. Its dependence on imported raw materials threatens long-term sustainability. Groyyo Consulting, a leading industry expert, steps in with a comprehensive solution – empowering Vietnam to achieve successful backward linkage, or domestic sourcing of raw materials.
Why Groyyo Consulting?
Groyyo Consulting isn’t just another consulting firm. Our team boasts veterans of the textile and apparel industry, veterans who live by their motto: “Grow With Our Expert’s Strategic Solutions”. This translates to a deep understanding of the intricacies of backward linkage and a commitment to propelling Vietnamese garment manufacturers towards a sustainable future.
Tailored Solutions for Backward Linkage Challenges
Groyyo Consulting offers a targeted approach, addressing the specific challenges Vietnam faces in achieving backward linkage:
- Building a Domestic Powerhouse: We assist domestic textile producers to establish or modernize their operations. We guide equipment selection, optimize plant layouts, and suggest production process improvements. Groyyo can identify areas for cost reduction, freeing up resources for investments in cutting-edge technology and crucial R&D.
- Quality that Commands Respect: Groyyo understands the importance of quality in a competitive market. We can ensure robust quality control systems within domestic textile production facilities. This includes training programs for workers, establishing quality management systems, and guaranteeing adherence to international quality standards. Additionally, Groyyo can help equip the workforce with the expertise needed to produce high-quality fabrics that meet the demands of global brands.
- Optimizing Within Existing Infrastructure: While Groyyo can’t directly address infrastructure development, we can help garment manufacturers optimize their supply chains and logistics within the existing framework. This may involve identifying alternative domestic sourcing options, implementing efficient inventory management practices, and leveraging technology to streamline communication with domestic suppliers.
- Building Strong Partnerships: Creating a win-win situation for garment manufacturers and domestic producers is key. Groyyo’s can help facilitate the development of strategic partnerships. This involves facilitating communication, establishing clear quality expectations, and negotiating mutually beneficial contracts. Groyyo’s can aid in creating online platforms that connect manufacturers with domestic suppliers, fostering transparency and efficient collaboration.
- Sustainability for the Future: Groyyo recognizes the growing demand for sustainable apparel by guiding domestic textile producers in adopting sustainable practices. This could involve implementing water-saving dyeing techniques, sourcing organic cotton, and minimizing waste generation. Additionally, help support the development of innovative, eco-friendly fabrics, catering to the future of fashion.
Conclusion
Groyyo Consulting is more than just a consulting company, we are a strategic partner in Vietnam’s garment revolution. Our comprehensive suite of services empowers Vietnamese garment manufacturers to foster a thriving domestic textile sector, enhance product quality, and ensure long-term sustainability for Vietnam’s garment industry. As Vietnam strives to become a global leader in sustainable garment manufacturing, Groyyo Consulting stands ready to be a valuable partner on the path to a brighter future.
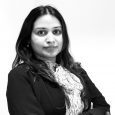
Leave a Comment