The apparel industry, renowned for its vibrant creativity and fast-paced innovation, is also deeply rooted in tradition. This dichotomy is particularly evident in the training methodologies used for sewing supervisors in manufacturing facilities. Many of these training programs are legacy systems, developed decades ago and no longer relevant to today’s dynamic and technologically advanced industry. To maintain a competitive edge and ensure operational excellence, it is crucial for the apparel industry to update and rejuvenate these training programs. Here’s why:
- Adapting to Technological Advancements
Modern sewing operations have been significantly transformed by technology. Automated sewing machines, AI-driven quality control systems, and advanced pattern-making software are becoming commonplace. However, legacy training content often fails to incorporate these advancements, leaving sewing supervisors underprepared. By developing new training programs that include the latest technological tools, supervisors can enhance productivity, maintain higher quality standards, and reduce downtime.
- Improving Productivity and Efficiency
Legacy training programs tend to focus on traditional methods and manual processes, which may not align with modern efficiency standards. Updated training content can introduce sewing supervisors to lean manufacturing principles, time and motion studies, and other modern efficiency techniques. These tools can help supervisors streamline processes, minimize waste, and boost overall productivity on the sewing floor.
- Enhancing Problem-Solving Skills
In an industry where rapid turnaround times are essential, sewing supervisors need to be adept at troubleshooting and problem-solving. Legacy training often does not emphasize these critical skills. Modern training programs can incorporate real-world scenarios, interactive problem-solving exercises, and case studies to enhance supervisors’ ability to quickly identify and resolve issues, ensuring smooth production flows.
- Emphasizing Quality Control
Quality control is paramount in the apparel industry, where even minor defects can lead to significant losses. Legacy training programs may not sufficiently cover modern quality assurance practices. New training content can educate sewing supervisors on the latest quality control techniques, including statistical process control, Six Sigma methodologies, and the use of AI for defect detection. This focus on quality will help maintain high standards and reduce the rate of returns and rework.
- Fostering Leadership and Communication Skills
Sewing supervisors are not just technical experts; they are also leaders who need to manage teams effectively. Legacy training often overlooks the importance of leadership and communication skills. By incorporating modules on team management, conflict resolution, and effective communication, new training programs can help supervisors build strong, cohesive teams that work efficiently and harmoniously.
- Promoting Health and Safety
The health and safety of workers are critical concerns in the apparel manufacturing industry. Legacy training programs may not adequately address modern health and safety standards or the latest ergonomic practices designed to reduce worker fatigue and injury. Updated training can ensure that sewing supervisors are well-versed in creating a safe working environment, adhering to current regulations, and implementing proactive measures to prevent accidents.
- Supporting Sustainability Initiatives
Sustainability is becoming a non-negotiable aspect of the apparel industry. However, legacy training content often does not cover sustainable practices. New training programs can educate sewing supervisors on how to implement sustainable practices on the sewing floor, such as reducing fabric waste, using eco-friendly materials, and improving energy efficiency. This knowledge can help companies meet their sustainability goals and appeal to environmentally conscious consumers.
- Adapting to Workforce Diversity
The workforce in apparel manufacturing is becoming increasingly diverse. Legacy training programs may not address the nuances of managing a diverse team effectively. Modern training can include diversity and inclusion training, helping sewing supervisors to create an inclusive environment where all workers feel valued and respected. This can lead to higher job satisfaction and retention rates.
The apparel industry must transition from outdated legacy training content to fresh, contemporary training programs for sewing supervisors. By doing so, companies can ensure that their supervisors are equipped with the latest technological skills, productivity techniques, problem-solving abilities, leadership qualities, and sustainability practices. This holistic approach to training will not only enhance the performance of sewing supervisors but also contribute to the overall efficiency, quality, and competitiveness of the manufacturing facilities. The time to invest in the future of training is now, ensuring that the apparel industry remains agile and resilient in the face of ongoing changes and challenges.
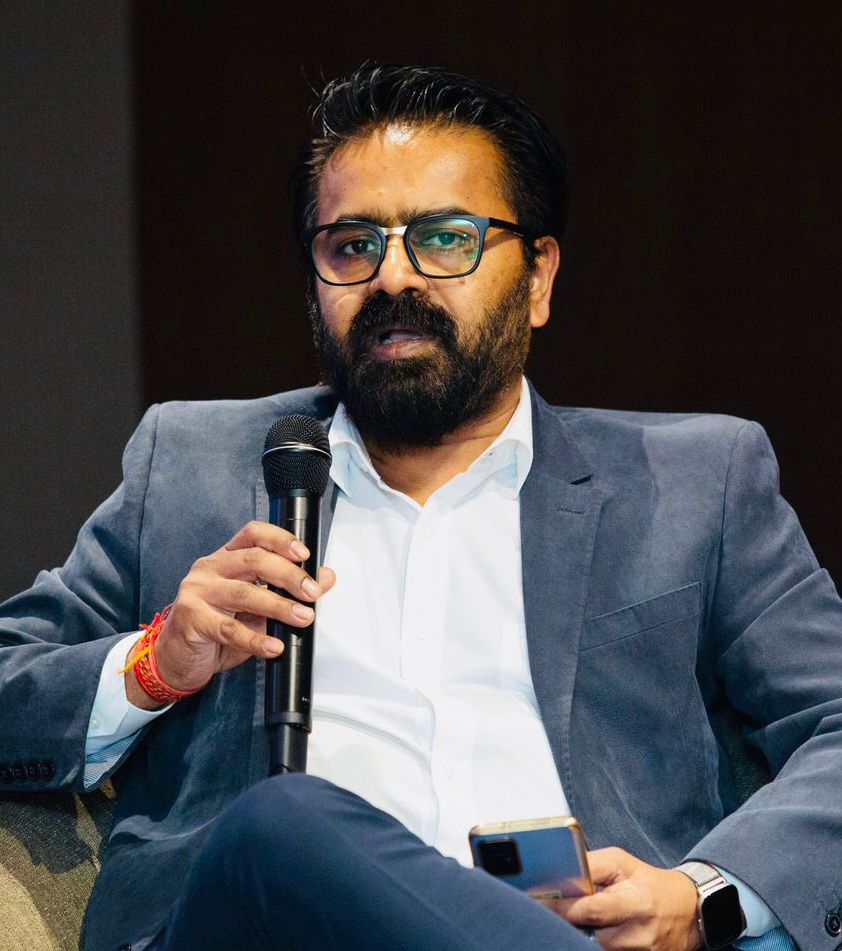
Leave a Comment