Global Apparel Manufacturing Industry: An Overview
The global apparel manufacturing industry is a vast and dynamic sector, serving as a cornerstone for economies worldwide. It encompasses everything from the creative design process to fabric production, garment manufacturing, and distribution, weaving together a complex supply chain that connects producers, suppliers, designers, retailers, and consumers. Major players like China, India, and Vietnam dominate the global stage, producing clothing for million
Technological advancements are reshaping the industry. Automation, artificial intelligence (AI), and the Internet of Things (IoT) are streamlining production, enhancing efficiency, and reducing costs. The global apparel industry was valued at $1.7 trillion in 2023 and is expected to grow at a compound annual growth rate (CAGR) of 4.5% from 2024 to 2030. E-commerce is a significant driver of growth, projected to expand at a CAGR of 6.3%, offering consumers greater convenience and accessibility. Consumers increasingly prioritize eco-friendly and ethically sourced clothing, prompting brands like Patagonia and Eileen Fisher to innovate.
Bangladesh’s Role in the Global Apparel Industry
Bangladesh is a key player in the global apparel market, ranking as the world’s second-largest exporter of ready-made garments (RMG) after China. In 2023, the sector contributed about $45 billion to the country’s export earnings, representing over 80% of its total exports. Bangladesh’s cost-effective production model, supported by a large labour force with some of the lowest wages in the textile industry, has made it a reliable supplier for global brands like H&M, Zara, Walmart, and Primark. Bangladesh has also made significant strides in sustainability, with over 200 LEED-certified green factories—more than any other country.
India’s Growing Apparel Sector
India’s apparel industry is rapidly expanding, with $44 billion in exports in 2023, focused on cotton garments, home textiles, and value-added segments like embroidery and handlooms. As one of the largest producers of cotton and synthetic fibres, India has a significant raw material advantage. India’s diverse portfolio appeals to markets in the U.S., Europe, and the Middle East.The Indian government has introduced initiatives such as the Production Linked Incentive (PLI) scheme and the Mega Integrated Textile Region and Apparel Parks (MITRA) program to improve competitiveness. However, challenges such as fragmented production systems, labour unrest, and logistical inefficiencies hinder growth.
Vietnam’s Rapid Rise
Vietnam has become the third-largest apparel exporter, with exports nearing $40 billion in 2023. The country is known for producing high-quality garments at competitive prices, attracting global brands like Nike, Adidas, and Levi’s. Vietnam’s strategic location and trade agreements such as the CPTPP and EVFTA provide preferential access to key markets, enhancing export potential.
Vietnam is investing in automation and sustainable practices to modernize its textile industry. Vietnam’s stable political environment and strong government support position it as a reliable player in the global apparel supply chain.
China: Key Players
While China leads in scale, automation, and innovation, it faces rising costs and geopolitical challenges. India capitalizes on its vast raw material base and cultural diversity but struggles with production fragmentation. Vietnam, although smaller, competes effectively by offering high-quality products, favourable trade advantages, and lower costs, capturing market share from both China and India. Together with Bangladesh, these countries form the backbone of the global apparel supply chain, each contributing unique strengths and facing specific challenges that influence the industry’s future.
Challenges Faced by Bangladesh’s Apparel Manufacturing Sector
Bangladesh’s apparel sector is poised for growth, with increasing adoption of automation, digital tools, and smart factory solutions. Sustainability is becoming a key focus, as global brands demand eco-friendly products. Bangladesh has the potential to lead in sustainable fashion while maintaining competitive labour costs.
Current Challenges
- Labor Dependency: The industry, heavily reliant on female labour, faced increased vulnerability due to workers’ socio-economic conditions. A study found 55% of workers had no savings, and many-faced household instability during the pandemic.
- Global Shifts: Global shifts in sourcing and competition from other low-cost countries pose a threat to Bangladesh’s position in global supply chains.
Despite these challenges, Bangladesh’s apparel sector remains vital to the economy, contributing 11% to GDP and achieving export growth from $5 billion in 2001 to nearly $40 billion in 2023.
The Evolution of Smart Factories Industry 4.0 technologies are revolutionizing global manufacturing, driving the shift to smart factories. By integrating automation, IoT, AI, big data, and advanced robotics, these factories enhance efficiency, improve quality, and reduce costs. For example, smart factories in manufacturing can adjust production schedules in real-time, minimizing waste. Sectors like healthcare and agriculture benefit as well, with better resource utilization and sustainability. The adoption of these technologies is expected to grow, allowing industries to innovate and stay competitive.
Smart factories reduce manual labour, boost productivity, and streamline operations in industries like automotive, healthcare, and food processing. Automation improves yield and reduces wastage, while AI and IoT enhance inventory management. Real-time data analysis optimizes operations, accelerating decision-making and production. In agriculture, sensors help manage resources sustainably.
Implementation approach on the Smart Apparel Factory:
- Conducting a thorough diagnostic audit of the manufacturing facility to comprehensively understand the processes involved from order placement to dispatch for all primary buyers.
- Revamping the processes and systems to align them effectively with the Supply Chain prerequisites of their primary clientele.
- Defining the optimal organizational structure based on the redesigned processes and systems, detailing departmental budgets and outlining clear job descriptions and key result areas (KRAs) for pivotal roles.
- Establishing an Industrial Engineering function to initiate Standard Allowed Minutes (SAM) based operations across all manufacturing departments.
- Implementing necessary reports to systematically record daily departmental performances in terms of time, quantity, and quality.
- Monitoring the performances of manufacturing departments and key team members based on agreed-upon Key Performance Indicators (KPIs) and KRAs.
- Introducing Daily, Weekly, and Monthly Management Information Systems (MIS) for enhanced process control, preferably integrating them within the ERP system.
- Suggest possible automation, folders, work-aids as per product category and feasibility.
Groyyo’s approach for Bangladesh Manufacturers to build a Smart Factory like Patronus Apparel
- Advanced Digital Infrastructure:
- Fully paperless operations, powered by robust Enterprise Resource Planning (ERP) systems and cloud-
based management tools like STITCH OS.
- Real-time data tracking for seamless production, inventory management, and quality assurance, enhancing operational transparency.
- Best-in-Class Machinery:
- Over 500+ high-performance automated machines majorly JUKI, integrating technologies and smart
systems for precision in CAD Tukatech pattern making, stitching, and cutting.
- Advanced equipment ensures reduced waste, improved efficiency, and superior product quality.
- Solar Energy Integration:
- A solar panel system installed of 107KVA across the facility’s expansive rooftop, harnessing renewable energy to power operations.
- This green energy initiative reduces dependency on conventional energy sources, lowering carbon emissions and operating costs.
- Sustainability at Its Core:
- Commitment to a zero-waste policy, incorporating eco-friendly materials and processes across all production stages. Like use of advance washing technology for less use of water as compared to traditional washing.
- Energy-efficient systems, including solar-powered lighting and HVAC (heating, ventilation, air conditioning) EVAPOLAR air cooling systems, further reinforce the facility’s environmental stewardship.
- Employee Empowerment through Technology:
- Ergonomically designed digital workstations enhance productivity and ensure worker comfort.
- Regular training programs help employees master advanced manufacturing technologies, fostering a skilled and future-ready workforce.
- Global Standards in Manufacturing:
- Fully compliant with international certifications for quality, safety, and sustainability, ensuring excellence in every product.
- A digital production line guarantees consistency, scalability, and the ability to meet diverse client demands.
Customer-Centric Approach:
- Digital dashboards provide clients with real-time production updates and seamless communication with manufacturing teams.
- Enhanced flexibility in design and delivery timelines caters to the dynamic needs of global apparel markets.
Revolutionizing the Garment Industry
Patronus Apparels Pvt. Ltd is more than just a factory; it is a vision of sustainable and tech-driven innovation brought to life. By integrating green energy solutions, cutting-edge machinery, and digital transformation, the facility sets new benchmarks for the garment industry. With its visionary approach, Patronus Apparels Pvt. Ltd not only leads in quality and efficiency but also champions sustainable future for global manufacturing.
A Vision for the Future
Hence we conclude, Smart factories represent the future of apparel manufacturing in Bangladesh. By integrating technology and sustainability, these factories can revolutionize the industry, ensuring it remains competitive in a rapidly evolving global landscape. Groyyo Consulting’s innovative strategies offer a pathway for manufacturers to transition seamlessly into this new era, positioning Bangladesh as a leader in sustainable and tech-driven apparel production.
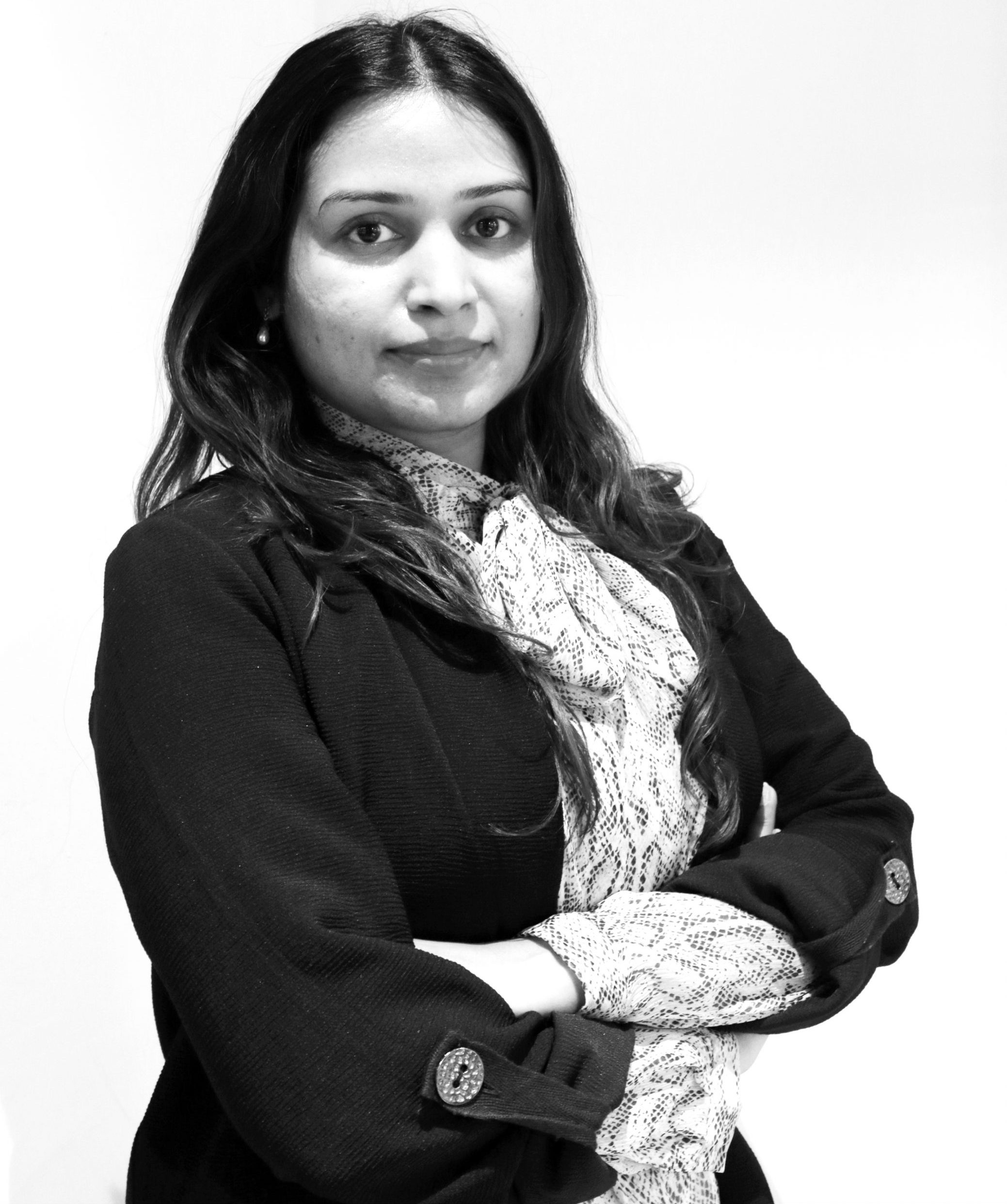
divyamohan@groyyo.com
Leave a Comment