The textile and garment industry is undergoing a revolutionary shift with the integration of digital technologies across the value chain. From design and raw material procurement to production and final delivery, digital transformation is creating a seamless, efficient, and customer-centric approach to manufacturing. Beyond operational enhancements, this shift is reshaping market dynamics, boosting product quality, and driving sustainability, enabling businesses to thrive in an increasingly competitive landscape.
Streamlining the Garment Manufacturing Process with Digital Tools
The garment manufacturing process traditionally involves multiple stages, often segmented and labor-intensive. Digital transformation is redefining each stage, addressing inefficiencies, and optimizing performance:
- Design and Product Development
Advanced digital tools such as 3D design software and virtual prototyping have revolutionized the design phase. Designers can now create, visualize, and modify garment designs in real time, significantly reducing sampling time and costs. Virtual samples also enable buyers to approve designs without the need for physical prototypes, shortening lead times and promoting sustainability by minimizing material waste. - Fabric Sourcing and Raw Material Procurement
Digital sourcing platforms allow manufacturers to connect with a broader network of suppliers, compare prices, check certifications, and monitor availability. These platforms streamline procurement by offering transparency and enabling real-time updates, ensuring that materials meet quality and compliance standards. Enhanced supplier collaboration reduces delays and ensures timely deliveries, which are crucial for meeting tight production schedules. - Production Planning and Execution
Cutting-edge Enterprise Resource Planning (ERP) systems and Manufacturing Execution Systems (MES) optimize production planning and execution. By integrating data from multiple departments, these tools provide real-time visibility into production workflows, machine utilization, and labor efficiency. Automated scheduling ensures optimal resource allocation, reducing downtime and improving productivity. - Cutting, Sewing, and Finishing
Automation in cutting and sewing processes, combined with data-driven insights, minimizes errors and maximizes precision. IoT-enabled devices monitor equipment performance and predict maintenance needs, ensuring uninterrupted operations. Quality control systems use AI to detect defects early, reducing rework and waste, while advanced finishing technologies enhance product consistency and customer satisfaction. - Inventory Management and Logistics
Smart inventory systems powered by AI and machine learning help manufacturers maintain optimal stock levels, avoid overproduction, and reduce holding costs. Real-time tracking systems improve logistics efficiency by monitoring shipments, ensuring on-time deliveries, and reducing transit losses. Integrated platforms also enable manufacturers to provide customers with accurate updates on their orders, enhancing transparency and trust. - Distribution and Retail Integration
Digital transformation extends to the distribution network, enabling manufacturers to collaborate with retailers and e-commerce platforms seamlessly. Predictive analytics and demand forecasting tools ensure that the right products reach the right markets, reducing unsold inventory and optimizing sales performance.
Driving Efficiency and Enhancing Market Value
The impact of digital transformation in garment manufacturing is profound:
- Faster Lead Times: Automation and real-time tracking drastically cut down production cycles, allowing businesses to respond quickly to changing market demands.
- Cost Optimization: Streamlined processes and reduced errors lead to significant cost savings across the supply chain.
- Higher Quality: Advanced tools ensure consistent product quality, which enhances brand reputation and customer loyalty.
- Market Agility: Predictive analytics empower manufacturers to anticipate trends, adjust production accordingly, and capture emerging opportunities.
Sustainability: A Strategic Priority
Digital transformation aligns closely with sustainability goals, addressing critical challenges in the industry:
- Waste Reduction: Virtual sampling, automated production, and optimized inventory management minimize material and energy wastage.
- Resource Efficiency: IoT-enabled systems track energy and water usage, helping manufacturers reduce their environmental footprint.
- Circular Economy: Advanced recycling technologies and data analytics support the use of sustainable materials and the creation of closed-loop systems.
The Future of Garment Manufacturing
The integration of digital technologies into garment manufacturing is not just a trend—it’s a transformation that is redefining how the industry operates. Businesses that invest in digital tools are equipped to handle future challenges, adapt to evolving market demands, and achieve long-term growth.
This end-to-end approach fosters innovation, sustainability, and resilience, positioning manufacturers to deliver superior value to customers while contributing to a more efficient and sustainable global market. As technology continues to evolve, so will the potential to create smarter, faster, and more responsive manufacturing ecosystems.
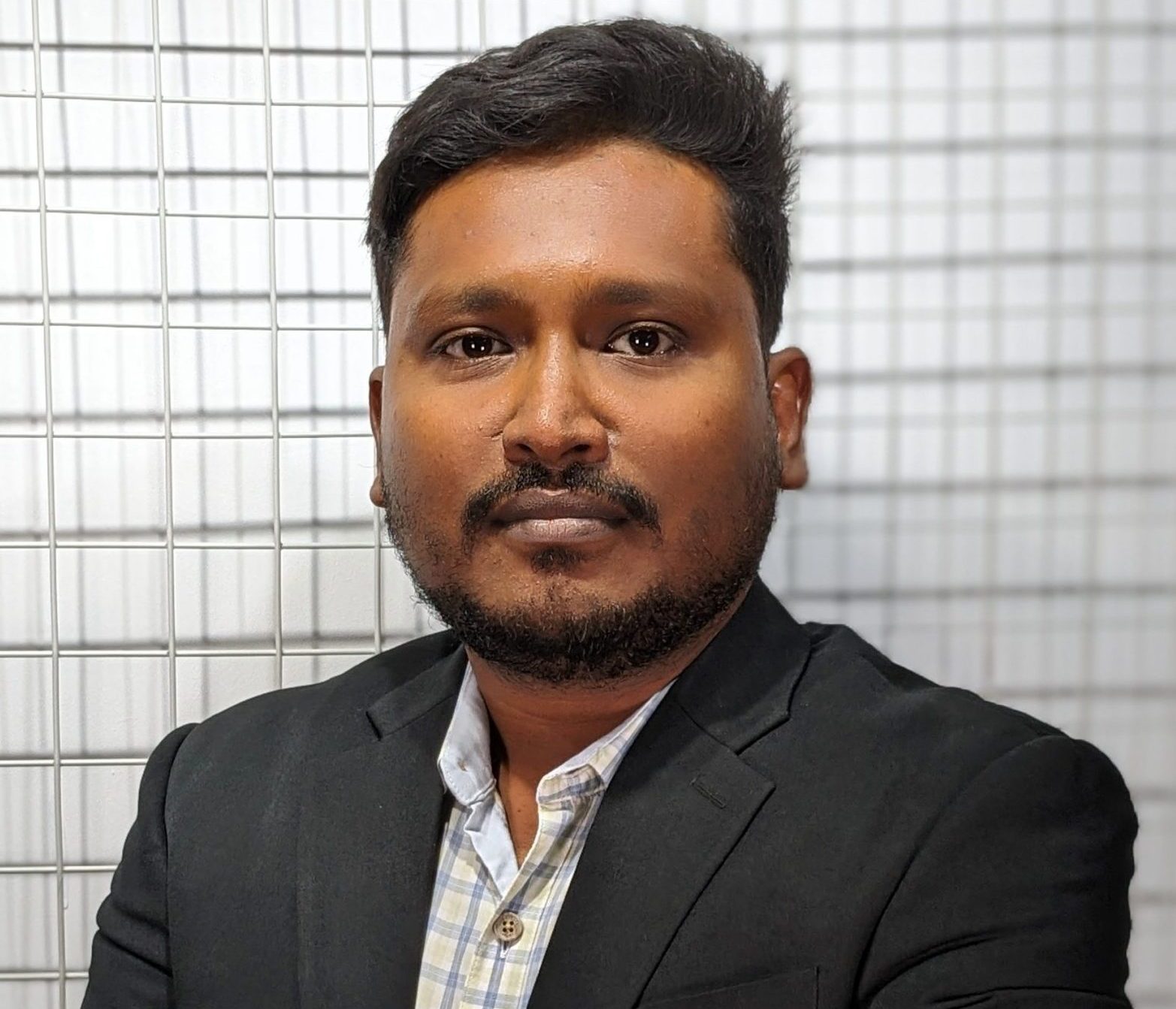
Leave a Comment