Vietnam’s apparel industry is a cornerstone of its economy, contributing over $40 billion in export revenue annually (Apparel Views, 2023). However, despite its impressive growth, many manufacturers in the sector have been slow to adopt digitalization, a key factor in enhancing operational efficiency and competitiveness. As global supply chains grow increasingly complex and buyer demands shift toward customization and faster turnaround times, digital transformation is no longer optional—it is critical for maintaining a competitive edge.
The Digitalization Challenge in Vietnam’s RMG Sector
Vietnam’s apparel industry is on the brink of a significant transformation, with many manufacturers recognizing the potential of digital tools to enhance their operations. As the sector evolves, there is a growing awareness that embracing digitalization can unlock new levels of efficiency and responsiveness to market demands. While currently, 35% of Vietnamese apparel factories have implemented digital production management systems, this presents a huge opportunity for growth compared to China’s 60% and Bangladesh’s 45% (VITAS, 2023).
Vietnam’s small- and medium-sized enterprises (SMEs) are particularly poised for digital advancements, as more affordable and accessible solutions become available. By adopting digital systems, manufacturers can streamline production planning, optimize inventory management, and enhance quality control. Moreover, the integration of data-driven decision-making tools will enable factories to achieve greater transparency, improve machine utilization, and track real-time performance metrics, positioning Vietnam as a competitive force in the global apparel market. The journey towards digitalization is not just a challenge but a promising pathway for Vietnam’s RMG sector to thrive in the future.
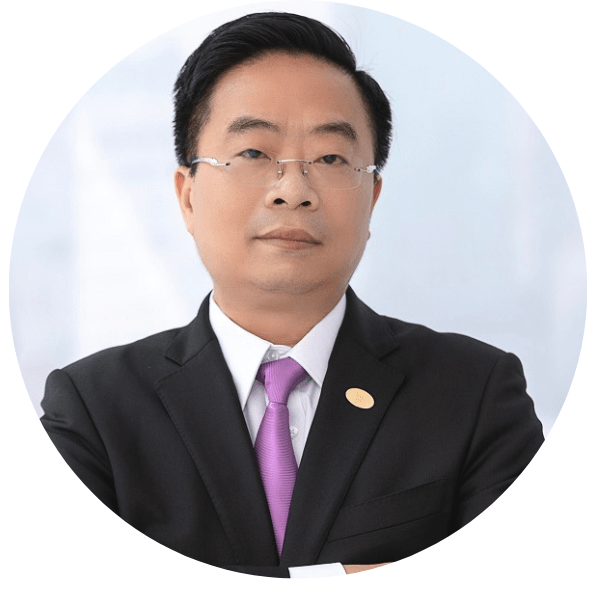
How Groyyo Consulting Can Assist Vietnamese Manufacturers
Groyyo Consulting specialises in guiding apparel manufacturers through the digital transformation journey, helping them leverage technology to improve operations, reduce costs, and increase competitiveness. By implementing cutting-edge solutions tailored to each client’s needs, Groyyo empowers manufacturers to unlock the full potential of digitalization.
Case Study:
1.Smart Digital Integration at Tarasima & Karim Textiles.
At Tarasima & Karim Textiles, Groyyo helped implement a comprehensive digital system to monitor and enhance operator performance. Through the use of automated tools, the factory was able to measure performance against standard targets, providing real-time feedback to the operators. This eliminated manual errors in data recording and resulted in a significant improvement in efficiency. Specifically, the factory assessed the skill matrix of over 2,500 operators, allowing for more accurate workforce management and productivity optimization.
Impact: Line balancing duration of the factory was reduced by 30 minutes.
2.Octorite Solutions for Himaya Apparels
In another instance, Groyyo introduced Octorite, an automated planning software, at Himaya Apparels. The solution streamlined the process of factory capacity booking and production order follow-up. This allowed for improved visibility into order statuses, reduced lead times, and optimised resource allocation.
Impact: The average production lead time was reduced by 15%, while overall factory processes were assessed digitally, resulting in reduction in idle time.
3.Transforming Supply Chain Management at Trance Home Linen
Supply chain transparency is a critical component of operational excellence. Groyyo assisted Trance Home Linen in digitalizing its inventory management and supply chain monitoring. Through the adoption of digital MIS (Management Information Systems), the factory could track all processes in real-time, improving cost efficiency and reducing errors in material handling.
Quantitative impact: The factory saw a 15% reduction in human defect rates, thanks to the digital tools that optimised labour allocation.
4.Enhancing Process Efficiency at Dolly J Pvt Ltd
Groyyo’s digital solutions also benefited Dolly J Pvt Ltd, where the introduction of a digital management system improved visibility across all departments. This holistic view allowed the factory to better manage upcoming styles and optimise manpower utilisation. Moreover, Groyyo’s integration of inventory management solutions reduced the chances of overproduction and minimised wastage.
Quantitative impact: The factory improved its inventory management and hence reduced the carrying cost by 14% and reduced material wastage by 5%, leading to significant cost savings and enhanced overall efficiency.
5.Capacity Expansion at Rue Fashions
At Rue Fashions, the implementation of Groyyo’s Octorite software led to significant operational improvements. Automated capacity booking and real-time production monitoring enabled the factory to optimize its processes and reduce overhead costs. As a result, Rue Fashions was able to increase its production capacity by 5% without additional capital investments, showcasing the power of digital tools in scaling operations.
Quantitative impact: The factory increased production capacity by 5%, while overall costs were reduced by 10% through optimized resource management.

Benefits of Digitalization for Vietnamese Manufacturers
The case studies above demonstrate how digitalization can drastically improve the performance of apparel manufacturers. By embracing digital solutions, manufacturers can benefit from:
- Improved Operational Agility: Automated processes allow manufacturers to respond more quickly to changes in demand and production schedules, reducing lead times and enhancing customer satisfaction.
- Data-Driven Decision Making: With access to real-time data, factories can make more informed decisions that improve productivity and cost efficiency.
- Supply Chain Transparency: Digital tools enable manufacturers to monitor every aspect of their supply chain, from raw material procurement to final product delivery, ensuring timely deliveries and optimal inventory levels.
- Cost Efficiency: By automating processes and reducing human errors, manufacturers can lower production costs while improving output quality.
- Sustainability: Digitalization also supports sustainability goals by reducing waste, optimizing resource usage, and improving energy efficiency, which is increasingly demanded by global buyers.
Conclusion: Groyyo’s Role in Leading Digital Transformation
Groyyo Consulting’s proven track record in integrating digital solutions for apparel manufacturers highlights the immense potential for operational excellence. As Vietnamese manufacturers seek to remain competitive on the global stage, Groyyo’s expertise in digital transformation offers a pathway to improved efficiency, cost savings, and market adaptability. With the right digital tools in place, manufacturers can transform challenges into opportunities, ensuring long-term success in a rapidly evolving industry.
In conclusion, the future of Vietnam’s RMG sector lies in digitalization. By partnering with Groyyo Consulting, manufacturers can unlock new levels of operational excellence, positioning themselves to thrive in the global market.
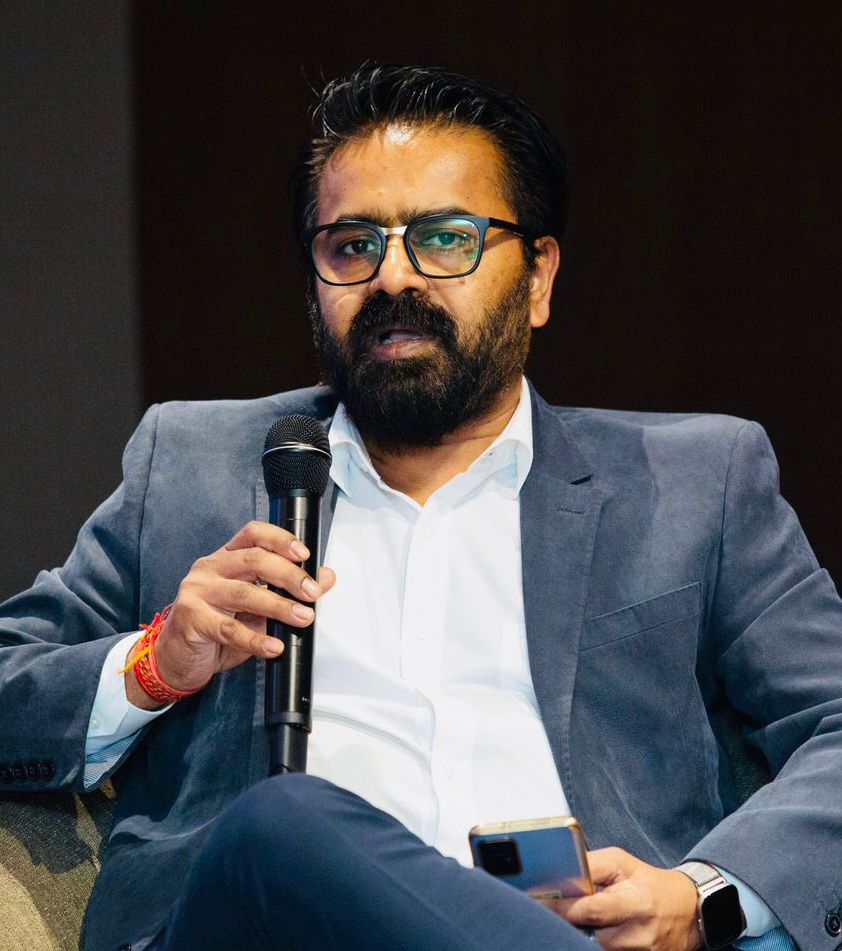
Leave a Comment